While Conco is justifiably proud of breaking the World record for the largest continuous mat pour, we are even more proud of doing it safely. Our commitment to safety began with the vision from Conco’s Southern California General Manager, Rick Parker. Five months prior to the pour, he invited John Messing, Conco’s Safety Director, to participate in the planning meetings for the Grand Pour. Rick has learned from his years of experience that projects go more smoothly when the safety department is involved early-on to ensure that safety is built into the overall work plan.
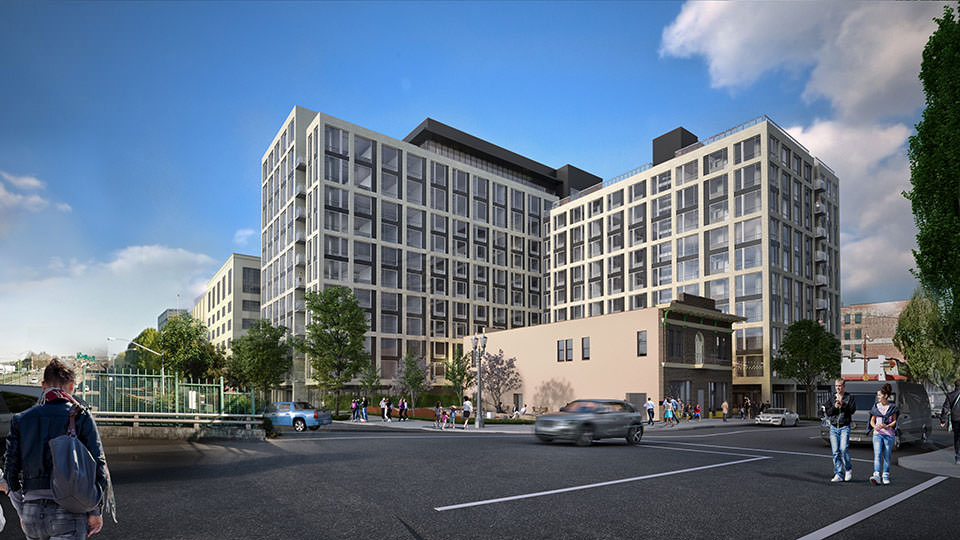
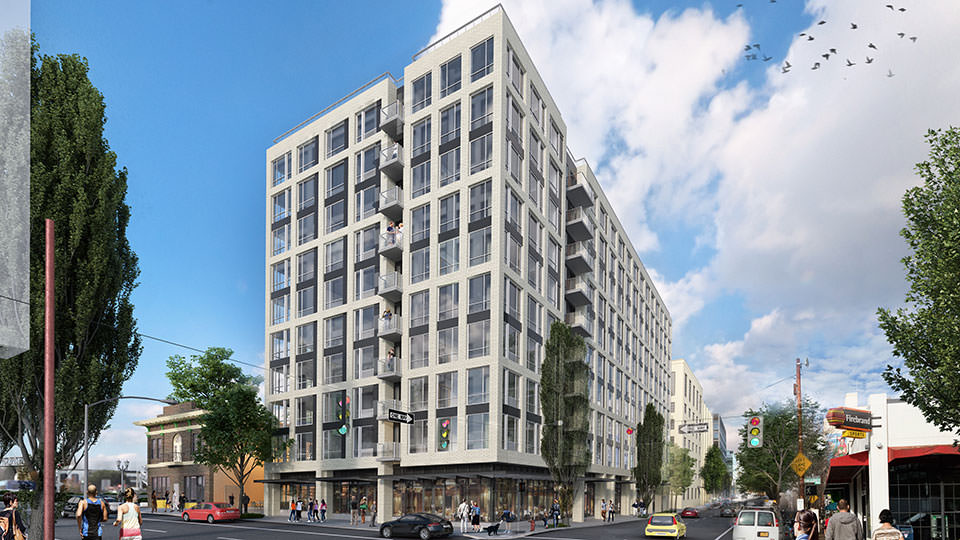
*Photos provided by Gary Leonard
Rick also made the prudent decision to devote the first-quarterly company safety meeting in January entirely to the safety of the pour. During the meeting, Rick Parker and Pumping Manager, Doug Marquis, provided an overview of the Wilshire Grand jobsite along with the challenges, unique project features, and logistical considerations of the job. John Messing spent the balance of the time devoted to discussing the importance of pre-task plans. He assigned three sub-groups to develop such plans regarding the work that they would perform. At the conclusion of the safety meeting, the pumping crew, place and finish crew, and street-level supervisors all had a unique, customized pre-task plan that was used as the basis to ensure their workers understood the hazards of the work and how to mitigate them.
The end result of the successful well-thought out plan was a highly professional team effort from all Conco employees. The entire team—at all levels—executed the plan to perfection, which resulted in zero injuries for this world record continuous concrete pour.